The need for fast internet and good connectivity is rising, and telecommunication aspects are increasing. Hence, the need to deploy fiber optic cable assemblies has increased with home and business uses. Pre-terminated fiber optic cable assemblies are provided to facilitate the seamless use of fiber optic cables. The present article will discuss and systematically discuss certain aspects of using pre-terminated fiber optic cable assemblies to minimize errors and make every time efficient. Once a technician implements the recommendations, everything will work as it should, there will not be any unnecessary downtime, and all work will be done economically and reasonably with no excess upfront costs.3
What is pre-terminated fiber, and why is it used?
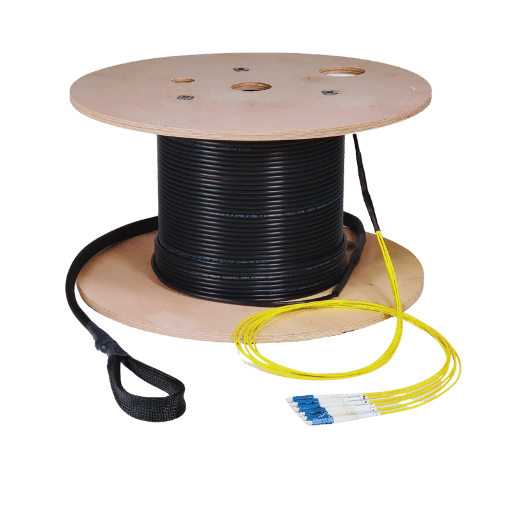
Understanding Pre-Terminated Fiber Optic Cables
Pre-terminated fiber optic cables are the types of cables that have all the required connectors already fixed on the fiber strands. This design avoids the necessity of field termination, which requires extra tools and skills. Praise is offered to the pre-terminated solutions as they are effective if they are to be deployed in data centers and office buildings as they require very little time and little hassle in setup. The most important advantages of pre-terminated fiber use are that the performer’s time considerably economizes in the process of its installation, and the chances of making wrong and inaccurate installation are minimal since the same practice has been reinforced. In all, pre-terminated fiber optic cables have promoted increased speed and scalability of network upgrades and thus have become much sought after in network applications of modern times.
Benefits of Using Pre-Terminated Fiber Assemblies
- Reduced Installation Time: Pre-terminated fiber assemblies take less time to install than field-terminated cables. Since the connectors are pre-terminated, not much work must be done on-site, so technicians can handle many projects effectively and quickly.
- Consistency and Quality Assurance: In place of assembly, a pre-terminated system of the optical fiber cable is prepared, which ensures that the provision of every point retains a constant quality. This results in increased reliability and performance and helps avoid situations where two connections made in the field, even if sealed, tend to have a higher incidence of failure.
- Lower Risk of Errors: When assembling on-site, pre-terminated systems’ installation avoids the site’s termination process, thus minimizing human errors like poor splicing or disconnecting wires. This is critical, especially in environments requiring performance to be at its best, such as data centers, as one mistake can cause a long loss period.
- Scalability and Flexibility: Pre-terminated solutions provide an easily installed and reconfigured network infrastructure. As business requirements change and evolve, these assemblies can be quickly altered or increased without a much-needed stoppage of operations and complicated installation procedures.
- Cost-Effectiveness: Although purchasing pre-terminated fiber assemblies is expensive, the return on investment is very attractive to organizations when combined with later labor cuts, reduced installation durations, and any future maintenance problems.
Typical Applications for Pre-Terminated Fiber
Pre-terminated fiber solutions are gaining popularity due to their efficiency and reliability in various industries and applications. Here are some typical use cases: Data Centers: In data centers, pre-terminated fiber assemblies offer rapid deployment and high-density connectivity even in cramped spaces, efficient cable management during installation, and flexible upgrade options for servers.
- Telecommunications: Telecommunications providers deploy pre-terminated solutions for network expansion and upgrade, which assists in the quicker launch of services while ensuring a very functional network and eliminating many of the risks present in effective new installations using traditional deployment techniques.
- Enterprise Networks: Many enterprises seem to have pre-terminated fiber for structured cabling installations. These solutions provide the possible integration of voice, data, and video systems, and they are not disturbing when it comes to the growth of network technologies.
- Campus Environments: Easy-to-install pre-terminated fiber systems are, for example, used in universities and corporate campuses, where quicker refurbishments and relatively simple reconfigurations are needed as the places tend to change or grow.
These applications exemplify the practicality and flexibility of pre-terminated fiber in further developing network structures with minimal interruption and high reliability.
How to Select the Right Fiber Cable for Your Needs
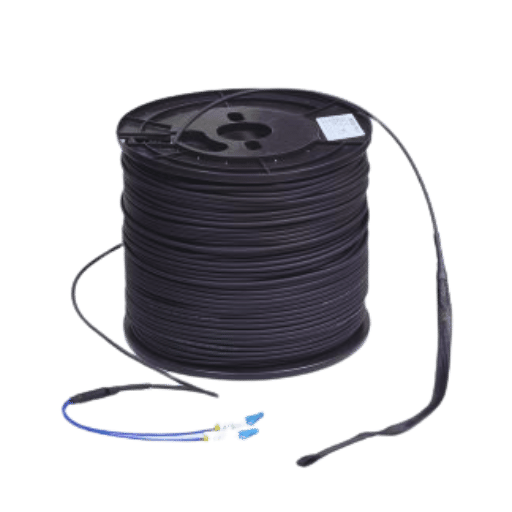
Different Types of Fiber Cables
There are different types of fiber optic cables, which can further be divided into single-mode and multimode fibers.
- Single-Mode Fiber (SMF): This type of fiber has a small core diameter of about 9 microns, allowing light to travel in a single mode only. It makes long-distance communication more efficient by minimizing signal attenuation while enabling high-bandwidth transmission over a longer distance. Therefore, it is suitable for both telecommunications and long-haul data transport.
- Multimode Fiber (MMF): Multimode fiber has a larger core diameter, usually 50 microns or 62.5 microns, and hence, it permits multiple modes of light to be transmitted through the fiber. Because of excessive modal dispersion, this type is typically used within shorter distances, such as inside buildings or within campuses. Concerning applications, multicore fiber has been found mostly in LAN enterprises as a good “speed” data application.
- Polarization Maintaining Fiber (PMF): This is a special type of fiber that preserves the polarization of light even after traveling long distances. This is useful in sensors and telecommunication applications where stability and accurate performance must withstand environmental disturbances.
All of them are fiber optic cables, but they have different usability purposes and performance levels. One should consider what decisions need to be made in a network.
Choosing Between Multimode and Singlemode Fiber
Choosing between multimode and singlemode fiber involves consideration of factors such as distance, bandwidth, and installation place. Multimode has become the standard type of cable used for shorter distances of up to 300 meters because it can handle multiple light-transmitting paths and, hence, is cheaper to install and equip than other fiber cables. It is ideal for local area networks where high speed is required, but the distances are limited. On the other hand, singlemode fibers are best used in long distances. These cables can, with high efficiency, transmit data over 40 kilometers with little signal loss, which is why this is the most preferred cable for telecommunication and facilitating the backbones in large networks. Besides, the total cost of installation also needs to be considered since singlemode cables could entail expensive components, whereas the components would be cost-effective in the future because of the robustness and high performance offered. All in all, the decision on the type of fiber to be used and the implementation methods will purely rely on the nature of the network to be equipped, how much it is expected to expand, and how deep into the pocket one is willing to go.
Understanding Cable Assemblies and Their Components
Cable assemblies consist of essential parts of fiber networks, such as optical fibers, connectors, and protective sheathing. Optical fibers carry light, and connectors provide a way to connect individual cutoff fibers, providing alignment within minimum signal loss. Components such as splice trays and strain relief devices that are incorporated are amenities finishing the cable assembly to enhance robustness and protect signal quality and reliability under various conditions. Attention must be paid to the proper analysis of the materials and the methods of the cable assembly process since they are the ones that determine the quality and working life of the cable assembly. A proper comprehension and selection of these components are necessary to achieve great performance and stability in the networks.
What Tools and Materials Are Needed for Installing Pre-Terminated Fiber?
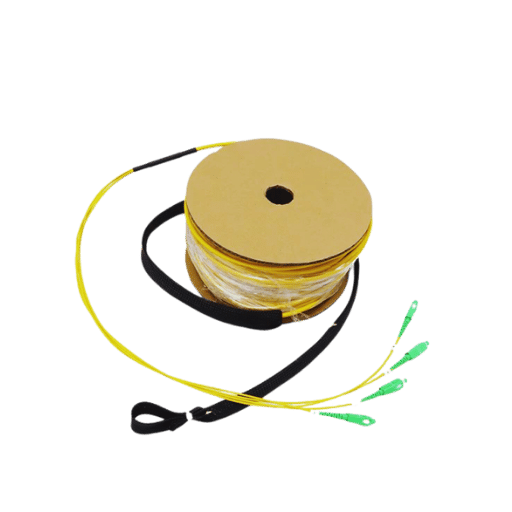
Using a SimpleGrip Fiber Cable Pulling Eye
The SimpleGrip Fiber Cable Pulling Eye is an important device that helps install pre-terminated fiber optic cables. This device efficiently manages long cable lengths, thereby inflicting minimum fiber damage. The pulling eye is usually made from robust materials and contains a provision for securing it to enhance easy cable pulling through constrictive conduits while preventing strain on the fibers. The user-friendly design improves productivity, hence making it an ideal device for the field. For optimal performance, it is essential to confirm the proper size of a pulling eye that fits the different cables and that the procedures used while attaching the eye are the best.
Necessary Tools for Cable Pulls
There are many different types of tools necessary for pulling cables for the fiber optic installation, which aim to make the process as efficient as possible and avoid breakages. These include:
- Cable Pulling Tape: This relatively light tape is used for pulling and guiding long cables over long distances, lowering their resistance and damage.
- Cable Puller: An apparatus that exerts force on heavy or long cables that require installation to facilitate easy installation.
- Fish Tape: A long, thin tool that can be bent and used to push or pull wires or cables through conduits and other small, closed spaces, preparing a space for running fiber optic cables.
- Cable Lubricant: Carrying the cable lubricant during installation makes it easy to pull cables out, reducing friction every time, especially on long runs.
- Safety Gear: Using apprehensible personal protective equipment such as hand gloves or protective eye gear is critical during the installation process.
Correct tool selection and usage improve the efficiency of installing optical cables and preserve the cables’ quality when pulled.
Additional Accessories and Attachments
Apart from the core tools required for fiber optic cable pulls, several additional items would greatly improve the installation process. These include:
- Pulling Eyes: These attachments assist in pulling the cable and provide a mounting point to which pulling eyes are attached. The pulling eye’s type and size should always be ensured to prevent overstress when being mounted.
- Cable Guides: Used to direct the cable’s angle during installation, these guides help avoid tangles, kinks, or crowding, especially around corners of loaded conduits.
- Cable Splice Kits: For projects involving wires that need to be spliced, it’s essential to keep these kits around. They contain all the accessories required for joining fiber optic cables with as little signal loss as possible.
- Tension Meters: These devices help the installer verify the amount of tension applied to cables when they are pulled. Correct tension should be maintained to prevent damage to the fibers.
Installers can use these additional accessories and attachments without compromising the structural integrity of the installation and outsmart the challenges associated with these fiber optical cable pulls.
How to Properly Install Pre-Terminated Fiber Cables?
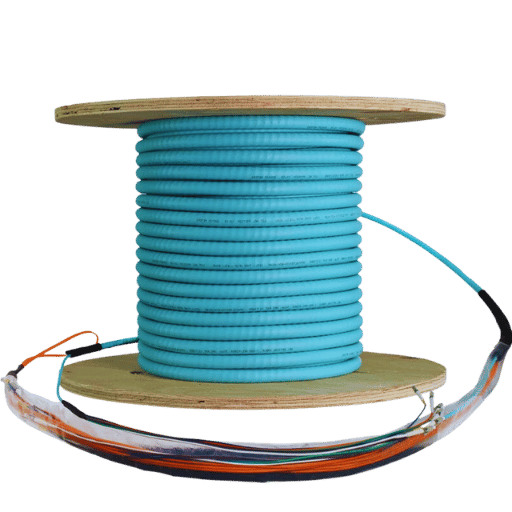
Step-by-Step Guide to Pre-Terminated Fiber Installation
- Preparation: Arrange all the needed tools and accessories to make the area clean and accessible. Check that the fiber cables, which have already been terminated, conform to the specifications of the available system.
- Cable Routing: We consider factors such as bends or other obstacles while planning how the wire schema will be laid out. In these steps, cable guides are deployed.
- Cable Connection: Attach the pre-terminated fiber cables to the appropriate sockets on the equipment as per the schematics. The end of piles and equipment connectors shall be clean, properly inserted, and turned to the mount position so as not to misalign.
- Secure the Installation: For any core cables that have to be pulled, use pulling eyes to prevent the connectors from being subjected to too much stress.
- Testing: After the final connections, continuity tests should be performed in accordance with the routine in order to check the signal transmission.
- Documentation: Collect information on how the installation was done, the type and length of the cables, the points joined, and the tests performed.
Reducing the number of terminations and making the cable installation process easier will ensure that pre-terminated fiber cables are installed reliably and effectively.
Tips for Using Conduits and Armored Fiber Cables
When installing conduits and other armored fiber cables, always keep the following technological recommendations in mind in order to improve performance optimization and safeguard the infrastructure:
- The Optimal Conduit Size Should be Chosen: In this case, the diameter of the duct or conduit shall be sufficiently large to accommodate the armored fiber cables as well as bends if any. This will help avoid the risk of damage and excessive friction during the journey.
- Choose High-Class Conduits. For environmental factors such as water, temperature, and impacts, choose conduits made of materials such as PVC or steel that can comfortably bear the factors of the environment.
- Provide for the Need to Grow: Provision of the extra space intended for additional conduit installation will go a long way toward allowing the installation of new technology without tearing up the existing space for future changes.
- Follow The Water Bendation: Follow the degree of bend and distance specifications given by the manufacturers when twisting the conduits so that you will not kink the fiber optic cable resting inside the conduit.
- Provide Endpoints With The requisite Protection: In respect of the above factors, it is essential to put on conduit end caps or bushings on the cable ends to protect them from the environment and damage.
- Schedule System checkups: Make sure that the conduit and armored cables are being inspected at regular intervals with proper wearing and damage. Therefore, if any such problem is encountered, it is cherished, and the functionality level is efficient.
So long as the guidelines are observed, installers will take care to wire in the conduits and armored fiber ropes properly, which will help protect the installation throughout its lifetime.
Ensuring Secure Connections with LC and SC Connectors
Some particular connectors, like LC and SC, need to be appropriately handled to facilitate secure connections. Seating the elements into position requires proper handling. Research indicates that debris on the surfaces just before the elements are mated will interfere with the signal. Attention should also be given to the second fiber when mating the connection or connectors to avoid the connection or connectors from being misaligned since it will degrade the performance of the fiber optic assemblies. For instance, users must be careful during the mating process, or excessive pressure will cause irreparable damage to the fiber ends and the connectors. You may also want to think about shielding or strain relief against physical forces at the termini in addition to strain relief. Lastly, the connection should center around regular checking and testing of optical power in and out of the connection to ascertain the performance according to the specifications.
What Challenges May Arise During Installation and How to Overcome Them?
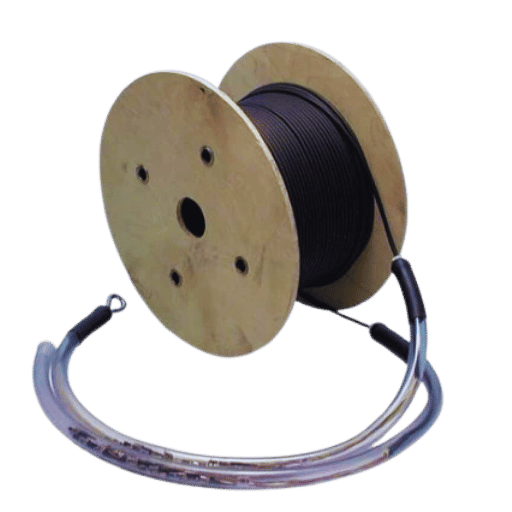
Dealing with Tight Spaces and Conduits
Several problems tend to occur during the routing of conduits and armored fiber cables in shallow wrapping spaces such as accessibility, maneuverability and the risk of damage. In order to solve these problems, it is suggested to follow these rules:
- Use Flexible Conduit Options: Furthermore, use conduits that are also flexible and can easily bend at the installation to facilitate the installation of the cougars and walls without damaging or deforming the cable’s structure.
- Employ Efficient Cable Pulling: Efficient forms of utilizing cable pulling specifically getting the corners out especially when the getting the corners is a problem like using a plasma or pulling lines are extremely helpful, Very no stress is exposed to the cables at all and no breakage occurs.
- Prioritize Planning and Layout: It is advisable to conduct a thorough evaluation of the space available, providing ample time for preparation prior to installation of the zip. Confirm that the tools and equipment are sufficiently placed, allowing enough universal design for installation of all in pump units, all separate, plus planning a systematic manner of execution.
- Utilize Appropriate Tools: Some specific working in confined spaces measures, such as palm drills, bend radii measurement tools, and right-angle heads, should be purchased. These tools aid greatly in accessing the site and help with accuracy as well.
By adopting these approaches, conduit and armored fiber cable installers in close-wrapping spaces will easily create space for such installations without compromising the utility and safety of the cables.
Troubleshooting Common Fiber Optic Issues
About fiber optics, it is essential to understand the cause of disruptions or underperformance. Some of the issues related to specific types of fiber optic cable usage include poor signal quality, worn-out connectors, and flexing beyond the cable’s minimum bend radius. Here are the essential measures that guide toward troubleshooting according to the industry standards:
- Signal Loss: In cases of excessive weather-influenced or otherwise induced signal loss, an optical fiber power meter with a light source may be used to probe and measure the strength of signals along the optical fiber. Fibers or fiber connectors with a contributing loss may also be removed and relocated where necessary.
- Connector Damage: Check for connection defects such as dislodged connections, a mechanical break, or dirt, oil, and fingerprints on the connector surface. Most of the time, the answers are pleasant and quick: the ease of cleaning the connectors with fiber optic cleaning systems brings them back to operational mode. If the connector breaks down, replacement is undertaken.
- Bend Radius Issues: Installation is done with bend radius requirements as specified by the manufacturer so as to prevent micro bending or macro bending, which generally leads to a high loss of signal quality. Here are possibilities: if bending is unavoidable, cable routing strategies should be used to minimize the chances of bent cables over their min. Radius.
These problems can be worked on, and thus, the fiber optic networks can function as they should.
Maintaining Cable Integrity and Performance
To maintain the integrity and performance of the pre-terminated fiber optic cable for a long time, proper installation and maintenance practices at agreeable intervals are necessary.
- Environmental Control: Fiber optic cables should be placed in areas where extreme temperatures and moisture are absent, as these will affect the cable’s protectants and cause improper functioning. For outside uses, such conduits are to be employed to prevent the effects of the weather.
- Regular inspections: Periodic inspection is an important factor in preventing further damage. Technicians should look into the damage, connector condition, and cable condition. It should be used in regoPatterns such as those of spinning devices or optical time domain reflectometric equipment regT. It is possible to determine some faults by regressing these stages in advance and in great detail.
- Procedural Compliance: It is important to abide by the manufacturers’ requirements regarding the activity done on the installed and maintained cables. These comprise the bend radius, which should never be exceeded, the details’ tensile strength, and the juncture characteristics’ lowest specifics. Proper technical and operational record-keeping should be done after installing and maintaining the systems to assist in monitoring performance and identifying problems.
Taking such measures within the acute time frame will enable organizations, most notably network providers, to realize an outstanding increase in fiber optic networks’ life span, availability, and data transmission performance.
Reference Sources
Optical fiber
Electrical conduit
Fiber-optic cable
Frequently Asked Questions (FAQs)
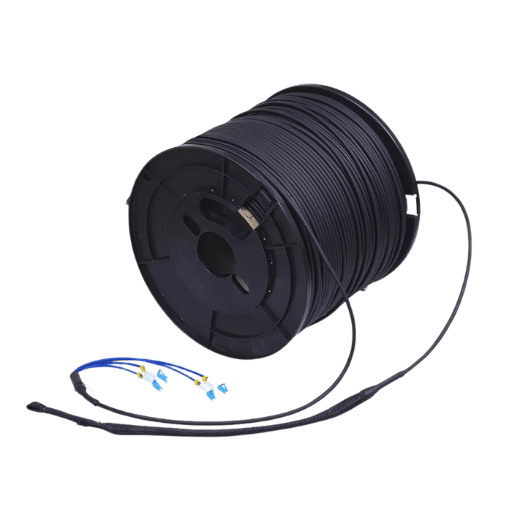
Q: What are the advantages of using pre-terminated fiber optic cable assemblies?
A: Pre-terminated fiber optic cable assemblies have several benefits, such as minimizing installation time and labor costs, reducing the likelihood of making mistakes in the field during termination, and eliminating the occurrence of poor quality and inconsistent terminations. Moreover, they are preferable when speed and effective performance are required, such as in enterprise networks and data centers.
Q: How do I choose the right fiber type for my pre-terminated fiber optic cable?
A: Selecting the right fiber type for your pre-terminated fiber optic cable is governed by many criteria, including run length, data rate, and the placement or installation environment of the cable. Common fiber types include multimode OM1, OM3, OM4, and singlemode fibers. In most high data rate applications, Multimode OM3 and service type om4 fiber optic cables are used in medium-distance installations.
Q: What should I remember when using pre-terminated fiber optic cables in plenums?
A: Regarding the question, the installation of pre-terminated fiber optic cables must be done with plenum-rated cables to meet the fire safety codes and requirements. Cables for plenum installation are insulated so that in the event of a fire, the cable would produce less toxic smoke and fumes, thus, more suitable in spaces that accommodate air passing through.
Q: Can I also deploy pre-terminated fiber optic cables for the outside?
A: Yes. Pre-terminated fiber optic cables can also be used for outside installations. However, selecting proper pre-terminated fiber optic cables for outside applications is critical. Such cables apply cross-linked polymers and jackets capable of resisting moisture, temperature, and UV. Armored fiber more or less works as a protective coat for the optical cables’ inner liquid.
Q: What are the most used connectors on the market’s pre-terminated fiber optic cable assembly?
A: Some of the pre-terminated fiber optic cable assembly connector types include LC, SC, ST, and FC connectors. The network requirements, such as the devices to be connected, how easily the switching device can be maintained, and whether future expansions are likely or not, will determine the connector to be used.
Q: What is the procedure for installing a pre-terminated fiber optic cable with an additional pulling eye?
A: If there is an additional pulling eye, first fix it to the pull string or hook and support the cable through a pull path. Then, insert the cable into the pathway or conduit without twisting or applying tension to the pulled cable. The pulling eye helps safeguard the connector ends during the pull-drag process.
Q: Why do some pre-terminated fiber optic cables find tight buffers essential?
A: For optical fibers, the tight buffer in pre-terminated fiber optic cables isolates the maximum mechanical stress an optical fiber may withstand. Installation becomes less stressful because every single fiber is protected. This is especially helpful when running the cables in elaborate routes or in enclosure boxes.
Q: What steps are necessary for adding premade fiber optic cables to a patch panel?
A: To terminate pre-terminated fiber optic cables at the patch panel, there are a few things that …1. Take the pre-terminated fiber optic cable to its respective patch panel location. 2. Fix the cable properly with cable management equipment. 3. Clean the ends of the connectors to improve optical effectiveness. 4. Put the connectors in the suitable adapters on the patch panel. As required, use precursor patch cords to join the patch panel to active equipment and the network.
Q: Why would it be proper to say that pre-terminated fiber optic cables are beneficial in scenarios that require fast installation?
A: Pre-terminated fiber optic cables are very fast to install because they can be directly used. They are factory terminated and tested, so there is no on-site termination and testing. All these help shorten installation, eliminate errors, and guarantee good-quality connection points. These materials are helpful for engagements that have hard deadlines but require high performance.
Post Views: 1,108