Using pre-terminated fiber optic cable assemblies is a big step forward in establishing high-speed communication networks. These cable assemblies are equipped with connectors during manufacturing, which makes them ready for use, thus minimizing installation time as well as complexity. The main objective of this post is to discuss the key components, advantages, and considerations related to pre-terminated fiber optic cable assemblies. It does so by looking at industry standards, installation best practices, and various applications that can be realized from them, hence giving readers an all-round comprehension of how these units can improve network performance plus reliability. Through this guide, whether you are working as a network engineer or contractor or just an interested person who wants to know more about current connection methods, you will be able to get the necessary background information needed for dealing with changes taking place within the fiber optics world.
What is a Pre-Terminated Fiber Cable?

Understanding Pre-Terminated Fiber and its Benefits
Pre-terminated fiber optic cables are a type of assembly that comes with connectors already installed, so there is no need to terminate them in the field. This feature is a major time-saver during installation because technicians only need to plug these cables into their existing network hardware. The advantages are lower labor costs, fewer mistakes made while setting up, and increased performance uniformity thanks to terminations done at a factory with better quality control. Furthermore, such pre-made connections make it easier for businesses or organizations to scale up their networks when required by allowing quick alterations or enhancements as per changing communication requirements.
Types of Pre-Terminated Fiber Optic Cables
To cater to various networking requirements, there are different configurations of pre-terminated fiber optic cables. Some of the main types are:
- Single-Mode Fiber (SMF): These fibers have a smaller core diameter hence allow only one mode of light to propagate making them suitable for long-distance communication. This in return leads to low attenuation which permits transmission over large distances thus being ideal for telecommunication networks and data centers.
- Multi-Mode Fiber (MMF): Having larger core diameters than single-mode fibers means that multi-mode ones support many modes of light propagation. Due to high modal dispersion rates, they are commonly used over short distances within buildings or campuses. There exist diverse categories of multi-mode fibers such as OM1, OM2, OM3, and OM4; each having different bandwidths and distance capabilities.
- Armored Fiber Cables: In order to withstand physical damages caused by harsh environments these cables possess protective sheathing around them. This makes them best suited for outdoor or industrial applications where cable integrity is key.
- Ribbon Fiber Cables: They consist of multiple fibers arranged in a flat ribbon-like structure which enables dense installations. Ribbons can be spliced en masse leading to significant reduction of splicing time thereby enhancing scalability within networks.
Knowing about these varieties will help network experts choose the right assembly among pre terminated fiber optics that aligns with their installation needs as well as performance targets.
Applications and Use Cases for Pre-Terminated Fiber Cables
Due to the simplicity of their installation and high performance, fiber cables that are pre-terminated have become popular across all industries. Some common uses include:
- Data Centers: The ability to deploy quickly and efficiently makes them ideal for environments with high-density where rapid scalability is needed. These connectors allow for immediate connectivity as well as cut down on installation downtime which can be crucial in maintaining operational continuity.
- Telecommunication Networks: For seamless connection between users and businesses, telecoms companies rely on pre-terminated fiber optic cables due to their speed and reliability. They are used in backhaul connections that enable fast data transfer over long distances with minimum signal loss.
- Enterprise Networks: Corporate settings make use of structured cabling systems based on pre-terminated fibers for network infrastructure improvement within different departments while allowing future expansion or upgrading without changing much physically because they support high-speed internet access among others.
Organizations can improve network performance, reduce installation complexity and ensure scalability by using pre-terminated fiber cables that integrate easily into evolving needs.
How to Choose the Right Fiber Optic Cable?
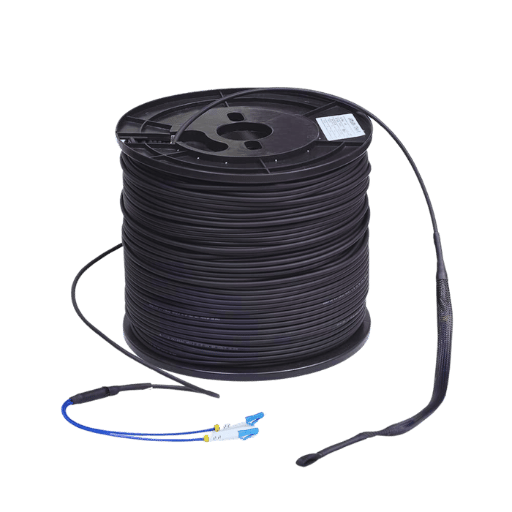
Differences Between Singlemode and Multimode Fiber
Single mode fiber optic cable has a small core only about 8-10 micrometers wide. This means that it only allows one light ray to be propagated at a time hence providing higher bandwidths and longer transmission distances of up to 40 kilometers or more. Also, because of having minimum attenuation this type is most appropriate for use in applications involving communication over very long distances.
Unlike single-mode cables, multimode fibers are designed with much larger cores ranging from around 50 to 62.5 micrometers in diameter, which enable them to accommodate many rays of light simultaneously. As a result, they can achieve higher data rates but only over shorter distances – up to approximately 300 meters maximum – due to modal dispersion that occurs when different modes disperse along the length of the waveguide, resulting in poor efficiency for long-distance communications.
To put it simply, single-mode fiber is an ideal choice for signals to travel far without losing quality, while multi-mode fiber optics work best when speed matters most within a limited area or building, etc.
Understanding LC Connectors and Other Connector Types
Fibre optic connector types like Lucent Connectors (LC connectors) have small form factors which can fit two fibres in the space of an RJ-45 used for standard ethernet connections. This means data centres and telecoms can have many more ports. Their precision alignment and low insertion loss mean they are also good for high-performance applications.
Subscriber Connector (SC) and Straight Tip (ST) connectors are popular too. SC connectors are slightly larger than LC ones but it’s their push-pull coupling mechanism that makes them so easy to connect and disconnect especially in high density situation where saving space is not much of a factor. ST connectors on the other hand use a bayonet-style coupling and were mainly used in legacy networks thus aren’t as widely used nowadays.
Ultimately, choosing your connector will be one step towards maximizing network performance because different types work better than others depending on what needs doing during installation process.
Choosing Between Plenum Rated and Riser Rated Cables
When it comes to choosing plenum-rated or riser-rated cables, one should have a grasp of where they are best used and what their fire ratings are. The plenum-rated cables are used in air handling spaces, for instance, ceilings or floors with heating and cooling ventilation. These cables do not easily catch fire since they are made of fire-resistant materials that keep off flames and reduce smoke production; hence, they are safe for crowded places. On the other hand, riser-rated cables should be installed vertically between different levels like ducts and conduits; while still being flame-retardant, these wires produce more toxic fumes than those meant for plenums during burning.
The decision on which cable type to go for has everything to do with local building regulations as well as the specific installation environment and safety compliance needs too. Not selecting the right kind of cable may compromise safety standards which must be followed strictly when setting up any network infrastructure.
Installation Processes for Pre-Terminated Fiber Optic Cables

Step-by-Step Guide to Installing Pre-Terminated Fiber Optic Cable Assemblies
- Evaluate Requirements: Figure out how long the cable must be, what type of cable to use, and where it needs to go in order not to interrupt anything that’s already there.
- Get Your Tools and Materials Together: Gather all the necessary tools like a wire cutter or stripper; also make sure you have everything else you’ll need such as junction boxes or mounting hardware.
- Prepare The Site: Remove any obstructions from around where you’re going to work and clean off your work surface. Check that your site meets safety standards according to local building codes.
- Run Cable Through Space(s): Thread through designated pathway(s) using preterminated fiber optic cables so they don’t bend too much which might weaken them by curving at too sharp an angle causing some loss in strength (attenuation).
- Make Strong Connections: Connect one end of each preterminated fiber optic cable into appropriate pieces of equipment while making sure all these things line up correctly with each other then plug another into its matching position on a patch panel; push until click/noise aligns the two halves securely together so no signal gets lost between them again.
- Check It Over With Some Tests: Use an optical power meter or light source for testing whether fibre connections are still good after installation by checking whether the light comes out intact enough at other end (which should mean no breaks). Also ensure signal is within required range.
- Record Everything: Keep track of all cables used including lengths as well test results achieved during setup; this will help if anything ever needs fixing later on.
- Finish Up: Put things back where they belong so they’re neat looking. Tie labels around cables near their ends so people know which is which without having to follow the entire length every time someone asks what something does/is connected to. Close openings securely behind covers while tidying away excess wire tightly against walls/floors/ceilings, etc.
Common Installation Challenges and How to Overcome Them
- Wrong Cable Routing: This can happen if you route them wrongly, and the result is potential signal degradation. Therefore, follow closely the setup plan while marking down clearly where these lines pass through.
- Physical damage to cables: Cables may get twisted or squeezed unknowingly during an installation process. Ensure that the way you handle cables follows the right procedure and use protective ducts if necessary so as to reduce chances of them getting physically damaged.
- Signal loss through poor connections: A lot of signal strength might be lost due to loose connections. It is important to have all connectors properly aligned and firmly tightened since this could greatly affect connection quality. While doing installation works always inspect joints regularly applying proper torque specifications.
- Environmental interference: Different variations in temperature together with moisture are some of external factors which can interfere with fiber optic performance. Such kind of cables should be selected that meet specific environmental requirements besides considering protection like climate controlled enclosures.
- Inadequate testing: Not doing enough tests after completing an installation can lead to undetected faults. Therefore, confirm whether performance metrics meet specifications before finalizing any particular setup by using dependable test gear and following standard test protocols for post-installation testing.
Tips for Installing Custom Pre-Terminated Fiber Cables
- Check Connector Compatibility: Ensure that the plugs on pre-terminated wires will fit into the devices they are supposed to work with. Look at both ends’ specifications and make sure they match each other.
- Determine Correct Cable Lengths: Measure the space where you’re going to install everything very carefully so there isn’t too much slack or tension in any cable. If lengths are accurate, connectors won’t have unnecessary pressure on them and everything will work better overall.
- Observe Bend Radius: Follow manufacturer’s recommendations for how big of a curve can be put in a line during setup. Bends that are too tight might cause some signal loss, so it’s important not to exceed suggested radiuses while aiming for best results.
- Label Cables Clearly: Use an easily understandable system when marking all of your new network’s wires. Being able to quickly identify which is which will help troubleshooting and future modifications go faster by cutting down time spent finding specific ones.
- Wear Protective Gear: Put on safety goggles or glasses when working around fibre optic cables to keep eyes safe from harm due to accidental drops or impacts. Also utilize edge protection anywhere conduits could pinch lines, thus shielding them from physical stress as well.
- Do Post-Installation Tests: Once finished, use an OTDR (Optical Time-Domain Reflectometer) or equivalent device for testing every link made during this process — it’ll verify integrity of signals & identify possible installation errors.
Maintenance and Troubleshooting
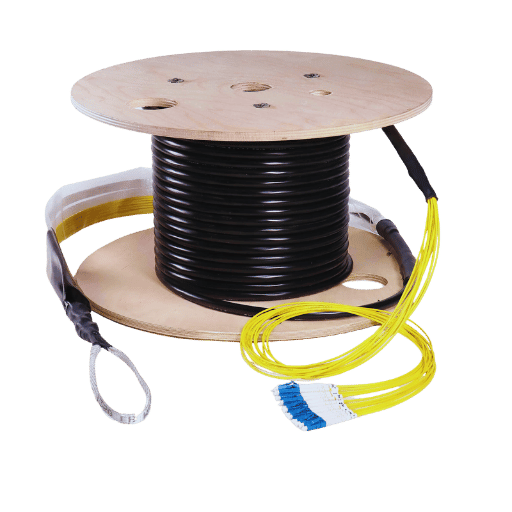
Maintenance Tips for Pre-Terminated Fiber Optic Assemblies
- Frequent Peer Observations: Perform regular checks visually so as to find out if there exist any physical mutilations on cables and connectors and keep them free from dust particles or other debris.
- Ensure Appropriate Storage: Place extra wires in a well-regulated area which is not exposed to extremely high or low temperatures that can damage their quality due to humidity change.
- Monitor for Overbending: Inspect installed cable systems for kinks with the help of adjustment tools where necessary in order to maintain specified bend radius limits.
- Keep Connectors Clean At All Times: Regularly clean up dirt on connecting ends using methods recommended by manufacturers since contamination affects signal transmission quality.
- Record Keeping Of Maintenance Activities: Keep accurate records detailing every activity done during maintenance such as checkups undertaken together with repair works carried out so that proper history can be tracked later on.
Common Issues with Fiber Optic Cable Installations
- Improper Connector Alignment: Signal loss and increased return loss can be caused by connectors that are misaligned. This is why it is important to ensure proper alignment during installation.
- High Loss at Splices: Splice loss happens when fibers are not well fused or cleaved. The problem can be solved by continuous training on best practices of splicing techniques.
- Physical Damage: Cuts, abrasions, or crushing may occur on cables in either installation or service environments. Physical damages can be averted through strict measures of protection coupled with regular checks.
- Overbending: Signal degradation takes place if cables are bent beyond their rated bend radius. Thus, installers must stick to the specified bend radius for maintained signal integrity.
- Contaminated Connectors: Dust particles or other dirt elements found on connectors have the potential to greatly affect the quality of signals transmitted over them. Therefore, they should always be cleaned as part of routine maintenance activities and handled correctly so as not to get dirty again.
- Poor Termination: More insertion loss may result from wrong termination methods being used. To guarantee dependable links, good termination practices must be followed together with appropriate tools selection for this purpose.
These common problems once identified and dealt with accordingly will greatly enhance reliability as well as performance levels achieved by fiber optic installations systems.
How to Repair and Splice Fiber Optic Cables
There are a lot of technical processes that need to be followed while repairing and splicing fiber optic cables so as to guarantee minimum signal loss and maximum performance. Some key steps outlined by professionals include:
- Damage Assessment: The first step is to find out how badly the cable has been damaged. This can be done through visual inspection or using Optical Time Domain Reflectometry (OTDR) for fault localization.
- Fiber Preparation: The protective jacket and buffer coating of the affected section should be carefully removed. It is necessary to do this using the right tools like fiber optic strippers in order not to damage the actual fibers.
- Fiber Cleaving: Once stripped, optical fibers must be cleaved so as to have a flat clean end face created. This step is very important because poor cleave can cause higher splice loss; therefore it requires precision which can only be achieved by utilizing cleaver tool.
- Fusion Splicing: Align cleaved fibers into fusion splicer where they are melted together by electric arc produced within it. Such method gives strong connection with low splice loss.
- Splice Testing: After splicing, it’s important that you test whether connection is good or not using OTDR or power meter which will help in identifying issues like splice loss among others if any.
- Splice Protection: When you are sure that your splice has been successful, put a protective sleeve over the joined area, making sure that it is well-fastened and sealed against any further damage.
These procedures enable technicians effectively repair fiber optic cables thus restoring connectivity with better performance. It also increases lifetime reliability for such installations when coupled with routine maintenance according to industry best practices in handling them.
FAQs about Pre-Terminated Fiber Optic Cable Assemblies
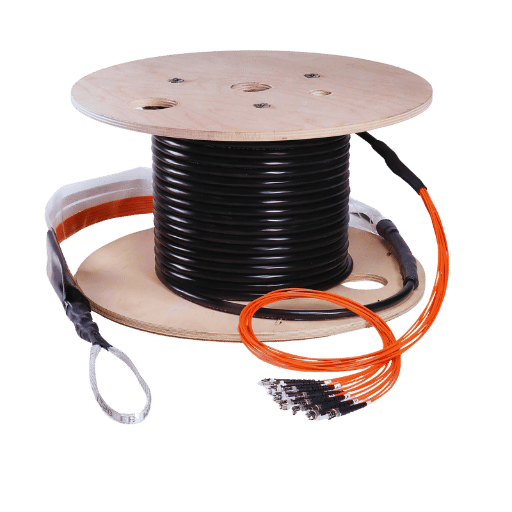
Why Use Pre-Terminated Fiber Optic Cables?
Pre-terminated fiber-optic cables have many benefits, such as saving time during installation and reducing errors on site splicing. They come with connectors attached so that deployment becomes faster while also improving connection uniformity. Furthermore, by ensuring terminations are done well in controlled environments, pre-termination can help lower the costs of installing a network and make its performance more reliable. Moreover, this method enables easy scalability and flexibility when changing or extending network infrastructures.
What is the Lifespan of Pre-Terminated Fiber Cables?
Pre-terminated fiber optic cables are designed to last between twenty and thirty years, contingent on a variety of factors such as installation conditions, environmental influences, and the commitment to maintenance. Less degradation may happen over time for cables that are installed correctly in managed environments with favorable conditions. Regularly checking for issues and fixing them right away will help these cable systems remain useful for longer periods, too; this means they will work reliably until their end of life when the network has been performing well during its entire service life.
Can Pre-Terminated Fiber Cables Be Used Outdoors?
Certainly, the outside environment is acceptable for pre-terminated fiber optic cables. They can be used outdoors if they are specifically designed for outdoor use. Normally, these cables are made of strong materials that can withstand harsh weather conditions, including moisture, temperature fluctuations, and UV exposure, among others. To guarantee the strength and long life span of fiber optics in challenging environments, it is important to choose those with appropriate insulation and jacketing that are outdoor rated. Furthermore, connection points should be made using suitable connectors, while enclosures help protect against any possible damage or performance dip over time, thus making an outdoor installation more reliable than when this is not done. With all these requirements met, from telecommunication networks to data center interconnections, many other applications may benefit from utilizing pre-terminated fiber optic cables outside.
Reference Sources
Optical fiber
Optical fiber connector
Fiber-optic cable
Frequently Asked Questions (FAQs)
Q: What is a pre-terminated fiber optic cable assembly?
A: A pre-terminated fiber optic cable assembly is a ready-to-use optic fiber that already comes terminated with connectors which make them plug-and-play. This makes it easy to install and does away with the need for splicing on site hence ensuring faster setup.
Q: What are the benefits of using pre-terminated fiber cable assemblies?
A: There are many advantages associated with using pre-terminated fiber cable assemblies including lower installation time, reduced labor costs, guaranteed performance and decreased chances of making mistakes. They can be most useful when connecting two buildings’ networks via an underground conduit or any other complicated scenario.
Q: Can I use pre-terminated fiber optic cable assemblies both indoors and outdoors?
A: Yes, pre-terminated fiber optic cables can be applied in both indoor and outdoor environments by customizing their outer jackets to suit different conditions so that they remain strong enough.
Q: What types of fibers are available in pre-terminated assemblies?
A: Single-mode (OS2) as well as multimode fibers such as OM1 are some examples of the various kinds of fibers which may come together with a given pre-termianted assembly based on what your network needs at that particular moment in time.
Q: How many strands can there be in a single pretermianted assembly?
A: Preterminiated assemblies commonly have different numbers of strands ranging from twelve through twenty four upto even higher counts depending on what is required by the network.
Q: What is the importance of the material used in making a cable outer sheath?
A: For durability, flexibility and protection, one must consider the jacket material of pre-terminated fiber optic cable assemblies. Safety and environmental requirements are met by using materials like OFNP (Plenum-rated) and LSZH (Low Smoke Zero Halogen).
Q: In a pre-terminated fiber cable assembly, what is meant by “breakout length?”
A: The term “breakout length” refers to how far apart individual fibers are from the main cable. This can be adjusted depending on installation needs so that different networks can be accommodated.
Q: Is there any customization available for pre-terminated fiber cable assemblies?
A: Yes, pre-terminated fiber cable assemblies may be customized for specific requirements. Customized options include fiber counts, connector types, breakout lengths, jacket materials, and cable lengths.
Q: What is a pulling eye used for in a pre-terminated fiber cable assembly?
A: A pulling eye is attached at one end of a pre-terminated fiber optic cable assembly to aid its installation. It serves as a strong point where the installer can hold when drawing the cables through conduits or other confined spaces without causing damage to connectors or fibers.
Q: How do pre-terminated fiber cable assemblies support gigabit Ethernet?
A: To enable high-speed data transmission between network devices; single mode (OS2) or multimode (OM1) fibers within them provide low latency as well as high bandwidth required for Gigabit Ethernet with this regard being considered ideal.
Post Views: 1,726