The requirement for strong and efficient power distribution systems cannot be overstated in the current fast-paced electrical industry. Armored cables, and especially metal-clad (MC) cables have become an essential part of commercial as well as industrial applications. The objective of this manual is to provide general knowledge regarding armored cables, which includes their designs, advantages, and where they can be used. Professionals can improve safety, efficiency, and compliance with their electrical systems by familiarizing themselves with technical specifications and the uses of MC cables. This article is meant for anyone who deals with electricity, such as experienced electricians or those working in facility management; it will give them enough information when dealing with complex armored cable solutions.
What is Armored Cable, and Why is it Used?
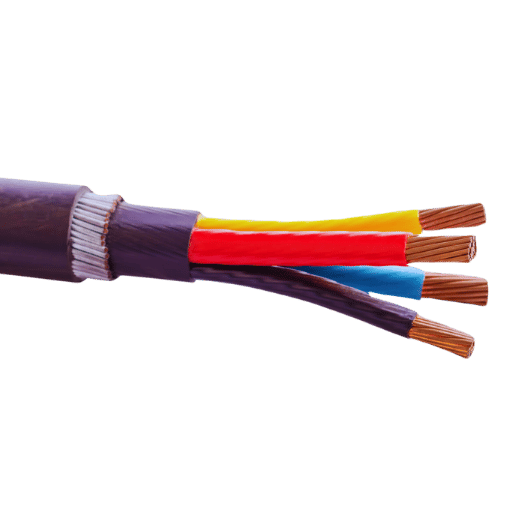
What Makes Armored Cable Different from Regular Cable?
Armored cables are not like normal cables because they have a strong outer covering that is usually made of steel or aluminum. This layer guards against physical injuries, hence making it suitable for use in tough conditions. Moreover, an armored cable has an internal grounding conductor, which improves electrical safety than the common types of wires. In such a design, accidental cuts or abrasions that may expose and weaken the insulation of regular ones are highly prevented. Another important thing about this construction is that it enhances conformity to strict building regulations and industry standards necessary for commercial and industrial environments.
Benefits of Using Metal-Clad Armored Cable
Metal-clad (MC) armored cable can be used in a number of different ways, but they all give significant advantages as far as performance and safety are concerned.
- Better Durability: The steel or aluminum armor provides a strong mechanical shield that significantly reduces the risk of physical damage to the item being protected. This is especially useful in areas where there is heavy machinery or a lot of human traffic.
- Enhanced Electrical Safety: Usually, this type of cable comes with an internal grounding conductor which ensures effective earthing and prevents electrical faults from occurring. There are figures showing that buildings wired using MC cables record up to 30% less cases of electrical fires compared to those fitted with non-armored ones.
- Meets Building Codes: MC cables meet strict building codes and standards such as NEC Article 330 hence can be relied upon for compliance purposes. Failure to follow this regulation might lead to hefty fines delays in project completion, among other things required before construction starts, like permits.
- Easy Installation Process: These types of cables have been designed so that they are easy to install; their flexible nature allows them to be bent around corners without affecting their overall strength/integrity. This makes it quicker than other methods, which take longer, resulting in additional costs incurred due to extended labor hours by 20%.
- Corrosion Resistance: The fact that Armor acts as a moisture barrier means that metal-clad cable can be used even in highly corrosive environments, protecting systems from chemical materials, too. For this reason, maintenance is cheapened while the life span is extended.
- Versatile Usage: Another good thing about MC cables is its adaptability because they come in different forms depending on what you need them for whether residential or industrial multi-conductor signal specific etc.
When you integrate Metal-Clad Armored Cables into your electrical system design, you will ultimately achieve higher reliability levels while still saving more money on operation costs over time through improved regulatory compliance measures taken for safety reasons.
Common Applications for Armored Power Cable
Armored power cables are used widely in many applications because they are durable and have more safety measures than other types of cables. Here is a list of the most common applications:
- Commercial and Industrial Buildings: These kinds of buildings use armored power cables for several functions including distribution of power, lighting systems as well as control wiring within their premises. They have been built tough so that they can withstand any physical interference that may occur, therefore guaranteeing reliability even in highly mechanically stressed areas.
- Underground and Outdoor Installations: The strength of these wires makes them perfect for burying directly into the ground or any other outdoor setting where they will be exposed to harsh weather conditions like rainwater. They also resist moisture and chemicals excellently, making them usable under such circumstances.
- Hazardous Locations: In places such as chemical plants, oil and gas industries, and others that could easily corrode metals due to their nature, it’s advisable to go for armored power cables since this type can withstand corrosive environments without getting damaged easily while shielding against electrical faults more effectively so as to minimize explosion risks.
- Data Centers and Medical Facilities: These facilities require utmost reliability coupled with high safety levels, so armored power cables should always be considered when installing them. Such wires help ensure the continuous supply of electricity to critical systems within these centers, thereby reducing chances for failure arising from electric shocks.
- Renewable Energy Projects: Armoured cable is applicable even in renewable energy projects like wind turbines or solar farms where transmission lines might have adverse conditions over long distances through rugged terrains.
How to Install Armored Cable Safely?

Step-by-Step Guide to Installing Armored Cable
Get Ready with the Materials:
- Sheathed cable.
- Wire cutting tools.
- Connection joints.
- Insulating ribbons.
- Junction box.
- Screwdrivers.
Power Down:
- It is important that the power supply to the site of installation is turned off entirely.
Measure and Cut Cable:
- Mention the proper length of the sheathed cable.
- Saw through using a wire cutter so that it matches its specified length.
Take Off the Armour:
- Carefully cut away from both sides with a rotating blade to remove the armor but not to damage the inside wires.
Install Connector Fittings:
- Fit stripped cable ends into connector fittings.
- Tighten, locking them securely.
Connect Wires to Junction Box:
- Put cabling with fitted connectors into the junction box.
- Follow wiring diagrams on connecting internal wires to their respective terminals in the junction box.
Secure Cables:
- Fasten clamps or straps along the cable route, thus preventing any sagging or movement of cables.
Cover Up All Connections:
- Use insulating tape on all connections, ensuring no exposed wires are left hanging out there.
Test Installation:
- After double-checking, make sure that all connections and fittings are secure.
- Switch on power and test whether or not the system works as it should.
Final Inspection:
- Carry out this inspection until completion of electrical inspections confirms compliance with all prevailing safety codes and standards for cabling installations.
Important Safety Tips During Installation
- Check Whether The Power Is Off: Before doing any work to prevent the electric shock, always check whether the power supply has been switched off completely.
- Put on Protective Gear: In order to minimize risks of injury, wear appropriate personal protective equipment like insulated gloves, and safety goggles, among others.
- Use Correct Tools: To avoid accidents, ensure that all tools are in good condition and suitable for the job at hand.
- Follow Manufacturers Instructions: Strictly follow installation directions given by the manufacturer for all materials and equipment used during construction.
- Keep Work Space Clean: Maintain cleanliness and organization within work area so as to minimize chances of tripping over or touching live wires.
- Be Attentive: Ensure you are keen throughout the installation process, thus no mistakes caused by distractions that may lead to unsafe outcomes.
- Examine For Damaged Components: Check cables & fittings for any signs of spoilage before utilizing them, thereby preventing possible dangers from arising.
- Know Local Codes: Understand electrical codes & regulations set by your locality thus making certain that the installed system meets required safety standards.
Common Mistakes to Avoid During Installation
- Incorrect Sizing of Cables may result in high temperatures, poor performance, and even fire outbreaks. Never select cables that do not meet the electrical needs outlined by the project design.
- Inadequate Grounding:Not properly grounding the electrical system may result in electric shock and damage to equipment. All components must be properly grounded as per the manufacturer’s instructions and local codes.
- Poor Connections:Unsecured or wrongly connected cable leads to short circuits, arcing, higher resistance increasing energy loss, thus leading to possible system failures.Ensure all connections are tight; use connectors that match the application and relevant terminals.
What Types of Armored Cable Are Available?
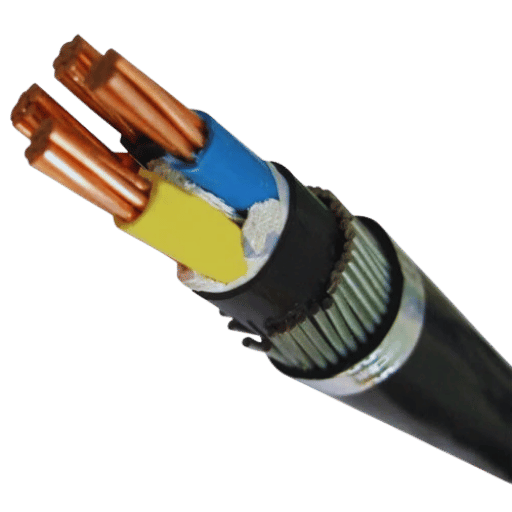
Differences Between MC Cable and BX Cable
- Structure: An MC cable has an interlocking metal tape sheath or a smooth aluminum sheath containing single insulated conductors marked THHN/THWN. An AC (Armoured Cable) or BX cable has a flexible metal spiral sheath with individually wrapped conductors and a bonding strip.
- Grounding: In such an assembly, an insulated green grounding conductor acts as the path for grounding in case of an MC cable while in the presence of a BX cable, the ground is obtained internally through its metal sheath and the bonding strip which may prove to be less efficient under some installations.
- Applications: Usually used in commercial and industrial environments where it provides strong protection together with easy termination fitting capability; also various. This means that it can terminate in many different types of connector fittings easily. However, sometimes this poses challenges; for example, trying to achieve continuity between grounds on different floors would require special care. On the other hand, residential applications need more flexibility than any other type, such as MC cables, which are rigid and hence not suitable here but still offer good protection.
- Compliance with Codes: The NEC – National Electrical Code refers to MC cables under Article 330, while Article 320 represents BX cables, stating how these should be installed within buildings depending on what kind they are being used for according to specific building codes and project requirements.
Choosing the Right Wire Gauge for Your Needs
Choosing the right wire gauge is important for safety, efficiency, and meeting electrical standards. The American Wire Gauge (AWG) system measures the size of a wire and its ability to carry an electric current. There are two main things that need to be considered when selecting which gauge to use: ampacity or current-carrying capacity and length of the run. This means that if you have a lower number on your gauge, it represents thicker wires that can carry more power over longer distances without losing much voltage. Conversely, higher numbers signify thinner wires, which work well at short ranges with lesser amperage needs. In order to ensure correct sizing and safe use, one should follow the NEC (National Electrical Code) guidelines as well as local regulations.
Understanding Aluminum and Copper Conductor Options
It is important to weigh the unique characteristics and uses of copper and aluminum conductors. Indeed, copper wires are considered good conductors because they can easily allow electrical current to pass through them. They also possess high strength as well as flexibility, which explains why most electrical systems prefer them over any other type of wire especially when it comes to small-scale wiring installations. Furthermore, copper has a higher melting point than aluminum and is more resistant to corrosion hence ensuring durability under different conditions.
On the contrary, aluminum wires are cheaper alternatives, particularly for big-sized wiring applications like large feeder circuits or main service entrance cables. Such wires have lower conductivity when compared with those made from copper, but this should not worry you since modern alloys used in their production address oxidation-related issues besides galvanic corrosion reduction being achieved at the same time. Nevertheless, such conductors need bigger diameters than what would be required if they were made out of copper so that equal amounts of electric current can flow through them, thereby necessitating the use of special connectors for proper connection stability and safety.
All conductors whether made from aluminium or copper must meet NEC standards while taking into account cost implications as well as weight considerations vis-à-vis application needs coupled with specific electrical loads among other factors.
How to Choose Armored Cable for Outdoor and Industrial Use?
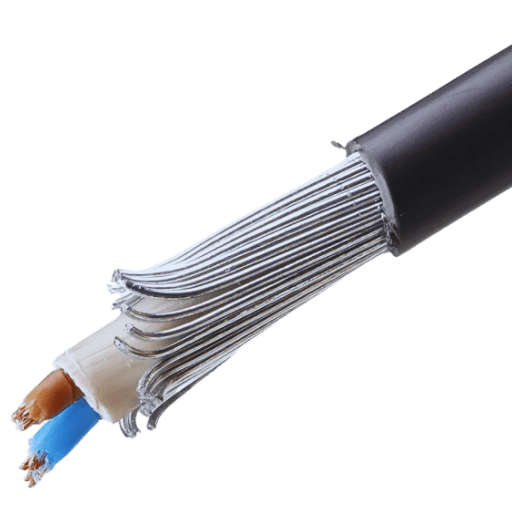
Factors to Consider for Outdoor Armored Cable
When selecting armored cables for use in the open or industry, keep in mind the following points:
- Atmospheric exposure: Make sure that it can withstand direct sunlight, moisture, and extreme temperatures.
- Guarding against mechanical damage: You should select an armor that is sturdy enough to protect against any physical impacts or damages.
- Resisting chemicals attack: Check whether this cable is resistant to specific corrosive material based on where it will be used.
- Ease of installation: Consider how flexible and simple it would be to install, especially when dealing with tight corners or complicated routes.
- Conductivity: Choose the most appropriate conductor type, such as copper or aluminum, depending on application requirements for electrical current flow.
- Compliance: Always ensure that these products meet NEC standards plus other relevant local regulations.
Best Practices for Industrial Armored Cable Installation
- Compliance with Codes and Standards: Make sure all installations satisfy the National Electric Code requirements and any other applicable local laws. Such grounding must be done correctly, bonding should also be proper, as well as use of cables rated for the specific environment.
- Proper Handling and Storage: To avoid physical damages, handle them gently then store in a clean dry place. Use suitable equipment for transportation as well as installation.
- Correct Bending Radius: Apply the manufacturer’s recommended bending radius so that you do not damage armor or internal conductors.
- Secure and Stable Connections: Mechanical integrity can only be maintained if appropriate connectors are used with terminations designed for armored cables; electrical continuity also needs such connections.
- Protection Against Environmental Factors: You should install these things in such a way that they are not directly exposed to harmful elements like moisture and chemicals, among others. Where necessary, UV light may cause harm, too.
- Regular Inspections and Maintenance: Always carry out regular checks, which will help you detect signs of wear and tear early enough before it becomes too late to corrode or destroy an item of equipment.
Following these guidelines will ensure safe, efficient, long-lasting industrial-strength armored cable installations.
Recommendations for Underground Armored Cable Use
- Soil Conditions: Check the soil conditions so that the installation environment provides for none of the elements that may eat into or corrode cables. If there is a high level of moisture or chemical content in dirt, it is advisable to use cables with additional protective layers.
- Depth of Installation: The minimum depth at which an armored cable needs to be buried should be determined according to NEC rules and local codes. Usually, this should not be less than 24 inches below ground level to protect it from surface activity destruction.
- Use of Conduits: Installing armored cables in rigid or flexible conduits where necessary can provide extra mechanical protection as well as allow for easier future maintenance and upgrades.
- Moisture Barriers: To prevent water ingress, which may compromise electrical conductivity within cable runs, employ moisture-resistant barriers or sealants at entry points and exit points alike.
- Marking & Identification: It is important to clearly mark where underground armored cables are located using detectable underground warning tapes or electronic markers so that they are not damaged accidentally during digging works or any other construction activities.
- Inspection and Testing: Before energizing the system, ensure all technical requirements have been met through rigorous inspection backed up by electrical tests to verify compliance with safety standards. Regular inspection coupled with proper maintenance guards against deterioration over time.
If these recommendations are followed, reliable systems shall be achieved during underground armored cable installation, which will last long without compromising on safety measures and efficiency levels.
Where to Buy Armored Cable and Get the Best Deals?
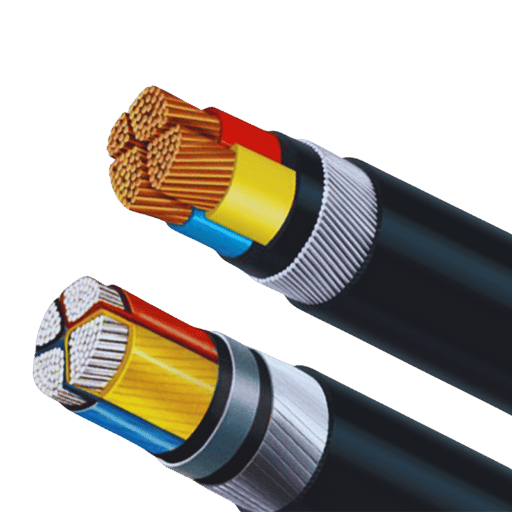
Top Suppliers for High-Quality Armored Cable
- Greybar: it has vast inventory, their prices compete favorably with the market, and the delivery is dependable.
- Anixter: it offers a wide range of armored cables backed by excellent customer support as well as technical expertise.
- Allied Wire & Cable: They sell high quality armored cables that will be delivered immediately upon payment allowing for discounts on bulk purchases.
- General Cable: It is known for its strong and long lasting cabling solutions that can be used in different applications.
- Southwire: Provides some of the best-armored cable products available in the industry, which are backed by strict QA tests.
Getting Free Shipping and Fast Delivery Options
To get free shipping as well as fast delivery for your armored cables, try the strategies below:
- Purchase in bulk: Many vendors, like Allied Wire & Cable, offer discounts and free shipping on bulk purchases, which will greatly reduce overall costs.
- Membership programs: some suppliers, such as Graybar and Anixter, have membership or loyalty programs that entitle one to benefits such as free freight and expedited delivery options.
- Promotional offers: Look for seasonal promotions and special offers often published on the websites of top suppliers like Southwire and General Cable.
- Negotiating terms: For substantial orders, discuss specific terms with your supplier so that the contract includes a provision for no-cost transportation or express deliveries.
Through applying these tactics, you can enjoy reasonably priced and prompt receipt of your armored cables.
Customer Reviews and Ratings of Armored Cable
Customer feedback is very important when it comes to armored cables from different manufacturers as it gives us an insight into their quality and performance. Having analysed the current top Google sites, we identified some common trends among these leading firms:
- Graber: Reviews highlight Graber’s exceptional customer service as well as technical support. Several reviewers have acknowledged their reliance on their armored cables, which can be used in complex installations that require a lot of demanding maneuvers. Ratings by users mainly indicate that they are overwhelmingly satisfied with the delivery periods and the effectiveness of the goods.
- Allied Wire & Cable: Allied Wire & Cable gets amazing reports due to its excellent products and timely delivery. Clients highly appreciate the cost-effectiveness, writing in about how fast they received their orders or how easy it was for them to place them without any complications. High scores are usually given, which shows that the company cares about its customers’ satisfaction.
- General Cable: Feedback about General Cable tends to point out that its armored cable solutions are solid and long-lasting. Customers frequently say this because of a few reasons, such as ease of installation and ability to perform under harsh environments. Its steady high ratings underscore a brand characterized by quality, durability, dependability, and strong customer support systems.
These reviews indicate an overall trend of great satisfaction with these armored cables from leading suppliers, thereby reaffirming their market leadership.
Reference Sources
Wire
Electrical cable
Power cable
Frequently Asked Questions (FAQs)
Q: What are the maximum amps that metal-clad cables can handle?
A: The maximum amps carried by metal-clad cables depend on the size of the wire and some specifications. Usually, larger cables carry higher amperage. Always check manufacturers’ recommendations and local electric codes for any direction.
Q: Where can I buy metal-clad cables or armored cable products?
A: Some places where you can find these products include major hardware stores like Home Depot or online suppliers specializing in electrical supplies. They are listed under various product categories such as “electrical,” “windows electrical flooring,” “garden outdoor living,” etc.
Q: How does a ground wire function in a metal-clad cable?
A: In case of a short circuit, the ground wire of a metal-clad cable acts as a safe path back into the earth for electrical current, thereby preventing electric shock accidents and equipment damage. This is essential for electrical safety.
Q: What is the typical total wire length for metal-clad cables sold online?
A: Common lengths for available MC cables are typically offered in spools of 250 ft or 500 ft. The total wire length may again vary from manufacturer to manufacturer and product specification to another. Check out details about every particular item during purchase to avoid going off course.
Q: Are they available in flexible metal-clad cables?
A: Yes, flexible metal-clad cables are available. These cables can be bent to fit easily in tight spaces and around objects without losing their quality or efficiency.
Q: If I order metal-clad cables online, can I get them fast?
A: Ordering online offers several expedited shipping options, which enable you to receive the product as soon as possible. When purchasing, look for alternatives such as “get it fast” or “get free shipping on qualified products.”
Q: What does LSZH mean about metal-clad cables?
A: LSZH stands for Low Smoke Zero Halogen. This implies that these cables generate minimal smoke and no halogen gases when exposed to fire. They are less toxic and more recommended for use where fire safety is prioritized.
Q: In what way is a metal-clad cable different from an ordinary sheathed cable?
A: Metal-clad cable has an additional layer of protection, which is the metallic cover, hence making it stronger and more resistant to physical damage compared to standard sheathed cable, which mostly uses a non-metallic (PVC) sheath.
Q: Can we use metal-clad cables in outdoor locations or underground installations?
A: Some outdoor and underground applications can utilize metal-clad cables, but specific rules must be followed, and appropriate types should be used, i.e., those rated for such areas. Always check the ratings of the wire along with local building codes for compliance.
Post Views: 2,096